In Australia’s competitive construction sector, achieving high-quality results while keeping costs under control is essential. Value Engineering plays a crucial role in this process. Rather than simply reducing expenses, Value Engineering focuses on optimising costs without compromising on quality or functionality. It’s a strategic approach that enhances project performance, boosts sustainability, and promotes collaboration among all stakeholders.
What is Value Engineering?
Value Engineering is a systematic process that aims to maximise project value by balancing cost, quality, and functionality. It involves a detailed analysis of all aspects of a project, from design to materials and construction methods, ensuring resources are used efficiently while delivering high-quality outcomes.
How Value Engineering Works in Australian Construction
Value Engineering is implemented throughout the project lifecycle, ensuring cost-effective solutions and optimal results. Here’s how it typically applies to Australian commercial construction:
- Analysing Project Functions The process begins by identifying the core functions of a project. This ensures that all elements align with project goals, enabling teams to make adjustments that optimise cost without sacrificing performance or compliance with regulations.
- Life Cycle Costing Value Engineering considers long-term financial impacts, focusing on sustainability, maintenance, and operational costs. By analysing energy efficiency, material longevity, and ongoing expenses, it ensures cost savings extend well beyond the construction phase.
- Strategic Material Selection Material choice is vital in Value Engineering. It emphasises using sustainable, locally sourced materials that offer the same performance at a lower cost. Additionally, selecting materials with lower maintenance requirements helps reduce long-term expenses.
- Innovative Construction Methods Adopting advanced methods, like modular construction or prefabrication, can reduce labour costs and construction time. Using Building Information Modelling (BIM) also helps identify potential issues before construction starts, reducing waste and rework.
- Optimising MEP Systems Mechanical, Electrical, and Plumbing (MEP) systems can be optimised for energy efficiency and reduced operational costs. This not only minimises initial expenses but also improves long-term performance, aligning with Australia’s sustainability requirements.
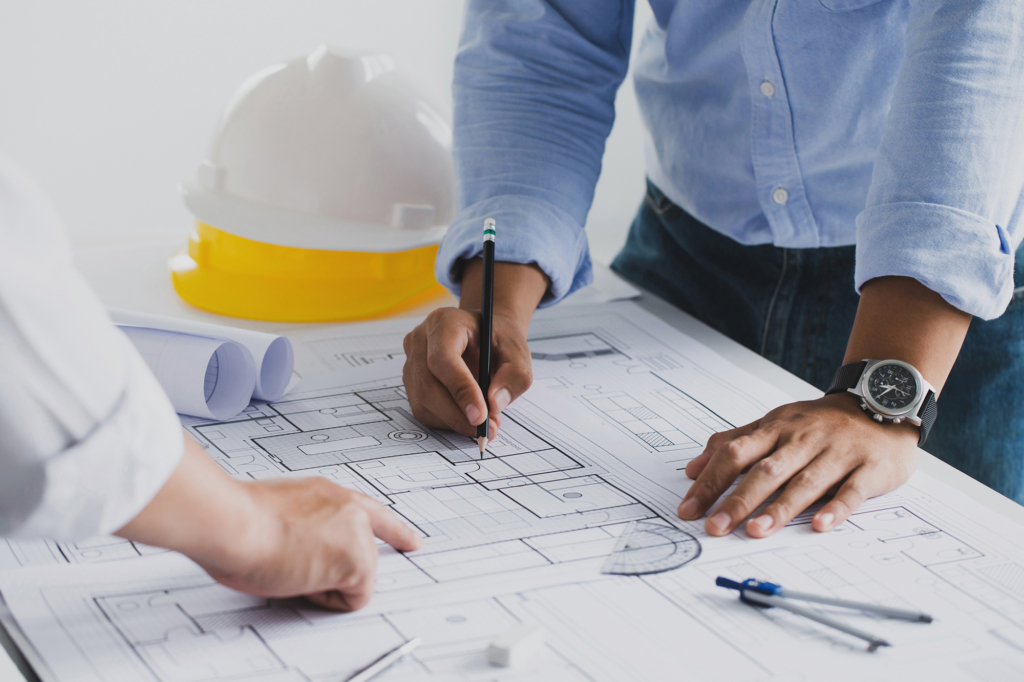
Benefits of Value Engineering in Australian Construction
- Cost Savings
Achieves up to 15% cost reduction through strategic design, material selection, and efficient construction methods. - Enhanced Performance
Improves project functionality by refining designs, optimising space, and boosting energy efficiency. - Sustainability
Integrates green solutions aligned with Australia’s eco-friendly initiatives while keeping costs manageable. - Better Collaboration
Promotes teamwork among stakeholders, ensuring well-informed decisions aligned with project goals. - Risk Reduction
Identifies potential issues early, preventing delays and cost overruns during construction.
Maximise Your Project’s Value with Buildland
At Buildland, Value Engineering is central to our approach. We apply it across commercial, residential, and industrial projects to ensure cost efficiency without compromising quality. Contact us on 02 7966 0200 or email info@buildland.au to learn more about how we can add value to your next project.